From Power-Plant Waste to Building Material Resource: A Circular Economy Success Story
By Matt Brownlee
Ensuring that sustainability goes hand-in-hand with quality in every construction product has never been more important than it is today. In fact, this is no longer something to which a company should aspire but a requirement for businesses to survive and thrive. At Holcim, providing innovative solutions to help customers meet their sustainability goals is integral to what we do and who we are. Our steadfast focus on taking a circular economy approach to doing business influences not only the essential building materials we provide our customers but also the way we make those materials.
To help preserve our nation’s natural resources and achieve a net-zero future, we are passionately committed to maximizing the beneficial recycling of waste by-products from other industries in our cement and concrete products. It is a win-win for our environment and economy.
Beneficial Reuse of Coal Ash
Coal is the fuel source for approximately one-quarter of electricity generation in America and produces large volumes of solid combustion waste—primarily fly ash and bottom ash. This ash from coal-fueled power plants is one of the largest types of industrial wastes produced in the US. However, it is also a waste product that is in high demand in the construction industry.
In fact, the term “waste” product is a bit of a misnomer when you consider the many reasons coal ash can be a valuable resource. Recycling it to produce cement and concrete, for example, dramatically reduces the consumption of virgin materials and the embodied carbon in building materials. For specifiers and concrete producers, fly ash in mixes delivers increased strengths and long-term durability of our nation’s infrastructure. For project owners, it helps them achieve LEED® certifications and other green building goals.
The Supply Dilemma
Sourcing supplies of coal ash has become increasing challenging for concrete producers and cement manufacturers due to the ongoing retirement of coal-fired power plants in the US. Trends indicate that supplies of this valuable resource will continue to decline as electric utilities steadily decommission their coal plants due to stringent environmental regulations and rising operating expenses.
According to American Coal Ash Association, only 59 percent of the 69 million tons of coal ash produced in 2020 was beneficially reused. The balance—28 million tons—was disposed in landfills or retention ponds. Considering the strong supply demands for construction applications, why is such a large volume of coal ash disposed in landfills? One reason is that demand tends to be seasonal following construction cycles. During slow periods, power plants fill up their storage capacities and send the remainder to landfills. The second reason is the injection of activated carbon into the combustion steam to comply with Clean Air Act requirements, which makes the fly ash unusable in concrete.
Meeting Market Demands
Over the last decade, the electric generation industry has shut down or announced plans to retire more than 65 percent of its coal-fired power plants in the US. Despite limited new construction and ongoing decommissioning of these facilities, the reduced volume of fresh coal ash can be offset by recovering these valuable materials from more than a thousand ash retention ponds and landfills facing federally mandated closure or remediation nationwide.
As the availability of coal ash continues to decline, harvesting the estimated 1.5 billion tons of ash currently stored in retention ponds and landfills holds immense promise to meeting the construction industry’s supply demands. Holcim and its Geocycle waste-management subsidiary are well positioned and actively engaged in meeting this need. Our pond ash recycling program with CenterPoint Energy is an excellent example of how we seek out win-win sustainability solutions with our utility partners that mitigate environmental risks for power plants while reducing the consumption of nonrenewable raw materials in building materials.
A New Life for Pond Ash
In 2019, Holcim, Geocycle, and CenterPoint Energy concluded an agreement on the largest excavation and beneficial reuse of ponded coal ash in the state of Indiana. This major recycling initiative represents the next phase in the long-term collaborative relationship between the companies. Since 2009, Geocycle has managed the ongoing supply of approximately 1.5 million tons of dry fly-ash waste from CenterPoint Energy’s A.B. Brown, F.B. Culley, and Warrick generating stations for producing cement.
The multi-year project at the A.B. Brown generating station encompasses the removal, conversion, and supply of more than six million tons of coal ash from a 165-acre pond for beneficial reuse at Holcim’s Ste. Genevieve cement plant—significantly reducing the facility’s consumption of natural raw materials, such as clay and sand. Holcim, Geocycle, and CenterPoint Energy invested on a combined basis over $80 million in infrastructure to remove, process, transport, store, and recycle the coal ash.
In late 2021, the project teams achieved a major milestone with the first barge shipment of 2,000 tons of the reclaimed material—containing mostly bottom ash with some fly ash—from the A.B. Brown facility. After processing at the Ste. Genevieve plant in Missouri, the quality of the pond ash was extremely high and there was zero waste in our cement manufacturing operations. We are now in the process of ramping up volumes for barging an estimated 400,000 tons of material in 2022.
With careful material sourcing and testing, this recycling initiative also advances the treatment of ponded coal ash for beneficial reuse in the production of more environmentally friendly concrete mixes. We are deploying this beneficiation technology, which included trials on CenterPoint Energy’s ponded coal ash, in select markets that are experiencing fly-ash shortages due to the ongoing retirement of coal-fired power plants.
A Reliable, Trusted Resource
While trends indicate less volume of coal ash, Holcim is committed to leading the way in boosting the supply of this valuable resource for a more sustainable future. Our success with the CenterPoint Energy program demonstrates that utilization of ponded coal ash is both environmentally responsible and economically feasible for meeting market demands.
With over 50 years of experience, Holcim has well-established and highly regarded coal ash programs with electric utility partners throughout North America. In addition to product supply through our world-class distribution system, we maintain a rigorous quality assurance program, rigid product standards, and strategically located technical centers and testing laboratories. To learn more, contact your local sales representative.
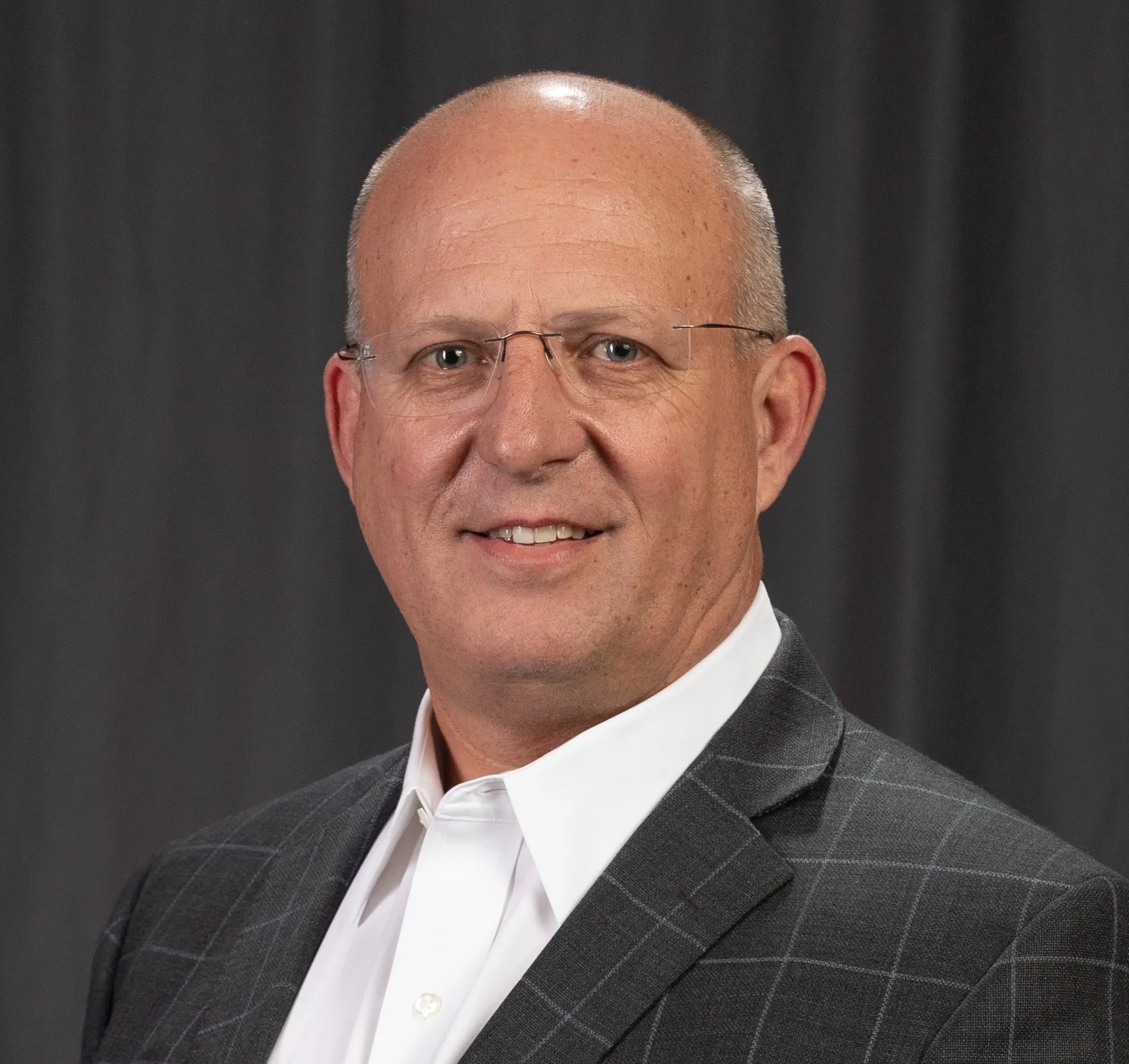
Matt Brownlee, Direct of Power Plant Services at Geocycle, LLC
Matt Brownlee is Director of Power Plant Services at Geocycle LLC, a subsidiary of Holcim (US). A 14-year business development and management leader of alternative raw material programs for Holcim in the US, Matt is a skilled strategist and expert in transforming the power industry’s coal-ash waste challenges into workable circular economy solutions for a more sustainable future. He holds a bachelor’s degree in Management from Charleston Southern University.