Slag Cement: A Valuable SCM to add to Your Concrete Toolkit
Today, slag cement (commonly referred to as slag) is regarded as an important part of the answer to the fly-ash spot shortages faced by ready-mix concrete producers, as well as the performance challenges faced by architects and engineers. Whether your needs call for general use, improved performance or durability enhancement, slag cement should clearly be regarded as a valuable supplementary cementitious material (SCM) in your concrete tool kit.
Holcim has been an industry leader in the slag cement business for many years. We have tremendous technical experience in developing innovative slag cement mixes and are strongly positioned to help you meet your supply demands for this important SCM.
More about slag cement
Slag cement is finely ground, granulated blast furnace slag (GGBFS), which is a by-product of the iron-manufacturing process. It has demonstrated compatibility with all types of portland cements, as well as with some combinations of fly ash or other SCMs. Slag cement can be used in concrete mixes either as a separate component or as a constituent of a blended cement (portland cement and one or more SCMs). It has been used in blended cements in the US since the late 19th century and has been available as a separate product since the early 1980s.
While slag cement and fly ash are commonly used and similar in many ways, there are some differences between these two SCMs. Understanding these similarities—and differences—are vital to developing optimal concrete mixes to meet the performance and sustainability goals of your next project.
Performance and Sustainability Benefits
Slag cement, like portland cement, is a hydraulic cement—it chemically combines with water to set and harden. Because slag cement has a more consistent chemical and physical structure than fly ash, it produces cement paste and concrete with more consistent performance results.
Utilizing high replacement levels of slag cement can reduce heat of hydration to help control shrinkage, creep and cracking in mass concrete structures.
Slag cement improves the properties of concrete in its plastic and hardened states. When properly proportioned in concrete mixtures, slag cement is particularly suitable for enhancing workability, increasing 28-day strengths, lowering permeability to chlorides, providing resistance to sulfate attack and alkali-silica reactivity (ASR), and producing a lighter, more pleasing color. Utilizing high replacement levels of slag cement can also reduce heat of hydration to help control shrinkage, creep and cracking in mass concrete structures.
As a recycled material, slag cement makes a significant contribution to sustainable construction. Its beneficial reuse in concrete mixes saves virgin raw materials, requires less energy to produce than portland cement, and recycles an industrial by-product material that might otherwise be disposed of in landfills. For projects seeking LEED certification from the US Green Building Council, the use of slag cement can contribute to credits in a variety of categories.
An industry perspective
The demand for slag cement is growing at a record pace in US markets. According to the Slag Cement Association (SCA), shipments in 2017 and 2018 increased 14 percent and 11 percent, respectively, from prior year levels. SCA Executive Director Drew Burns noted that they are seeing growth in all segments, especially infrastructure and mass concrete. “You can use a lot more slag cement in your mixes for infrastructure and mass concrete applications, so you can increase service life while also achieve cost benefits due to the high level of portland-replacement volumes,” he said. “In addition to fly ash shortage issues, increased awareness and understanding of slag cement’s reliable consistency and performance-enhancing qualities are also driving product demand.”
The short-term and long-term supply outlook for slag cement is good and there has been a noticeable uptick in the use of slag cement in certain regions. There is very good product availability in the Great Lakes, Mid-Atlantic, Northeast and Southeast regions, which have good supply networks in those areas. The Western region, however, has a much more limited supply. “There is a lot of interest and activity currently underway to bring slag cement into Texas, and a lot more slag cement is being used in the California market,” said Burns. “These continuing developments will open future supply channels to meet product demands in other Western states.”
Wide range of applications
Slag cement in ready-mixed concrete is used in architectural structures of all kinds, roads and bridges, precast/prestressed products, pipe and block, mass concrete, and a whole host of other applications. Below are highlights of some of Holcim’s 2018 award-winning applications that have been recognized by the Slag Cement Association.
Ottawa River Storage Facility
The Ottawa River Storage Facility (ORSF) was part of the Toledo Waterway Initiative. The project consisted of removing Joe E. Brown City Park (22 acres) and building a 36.3 million gallon storage tank underground, then reinstalling the park. Over 450,000 cubic yards of earth were moved. The storage tank consisted of a concrete floor, walls, columns and roof. Slag cement was used to prevent thermal cracking in the thicker segments of the floor, walls, and roof. It was also used to decrease the permeability of the concrete floor, walls, and columns and to provide sulfate resistance against the storm/sewage waste water. Slag cement helped achieve an average compressive strength of over 7,000 psi (5,000 psi was specified) in a 35% replacement mix with 500 lbs cementitious material at 0.42 max w/c ration.
This high-performance crossing over New York’s Hudson River was built to replace the Tappan Zee Bridge. The concrete for the towers, piles, columns, caps and piers needed to attain high strength, resiliency, and 100-year service-life goals. After rigorous performance assessments, the project team selected a 9,000-psi mix design containing 67% slag cement to achieve long-term durability, low heat of hydration, and excellent ASR mitigation and sulfate resistance.
The Holcim Advantage
While fly ash has long been considered the “go-to” SCM for many ready-mixed concrete producers and specifiers in US markets, slag cement’s combination of availability, performance and environmental benefits is quickly gaining converts. The growing trend for slag cement use in industry specifications—combined with fly ash spot shortages and increased need for quality SCMs—will further accelerate the demand for this valuable SCM in coming years.
Holcim’s technical and quality groups have led North America in the research and development of specifications for slag. Through our extensive production capabilities, quality-control laboratory network, and world-class distribution system, we are strongly positioned to meet your current and future needs for slag cement, as well as a variety of other SCMs.
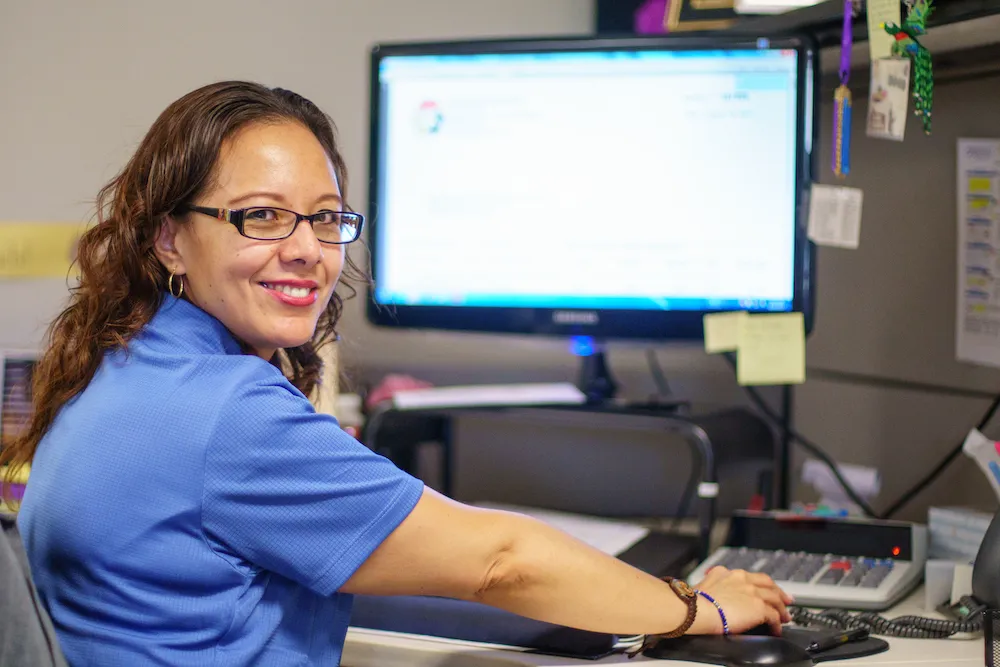
Have a question?
Our sales reps are ready to assist you with your project.