Building Greener, Building Better with Supplementary Cementitious Materials
By David Diedrick
Green building is a measurable and cost-effective solution to the complex challenges of climate change. The building sector is responsible for nearly half of the carbon dioxide (CO2) emissions in the U.S. and a significant portion of our world’s greenhouse gas emissions. How we construct and manage our buildings today will have a significant impact on our global environment for many decades to come.
Now and long into the future, sustainable construction will be in strong demand, resulting in significant economic, social, and environmental benefits. Holcim’s LEED®-accredited professionals and other technical resources have an in-depth knowledge of innovative cementitious material solutions and mix-design best practices to help you meet the growing calls for a high-performance built environment with a lower carbon footprint.
SCMs and blended cements
Supplementary cementitious materials (SCMs) offer sustainable and performance advantages for those who construct buildings of all kinds. Their use as a partial replacement for portland cement not only results in more durable, high-performance concrete but also lowers energy consumption and greenhouse gas emissions. For every ton of clinker replaced by SCMs, CO2 emissions are reduced by approximately 0.8 ton.
SCMs are utilized in concrete as a separate component or as a constituent of blended cement. The most common are slag (a by-product of iron manufacturing), fly ash (a coal combustion by-product from power plants), silica fume (a by-product of manufacturing silicon metals), and natural pozzolans (e.g., calcined clay, calcined shale, and metakaolin).
Cementitious blends have many properties that contribute to sustainable construction.
Their use results in stronger, longer-lasting concrete and reduced emission of greenhouse gases.
Considering that concrete is the most widely used construction material, cementitious blends can have a major impact on the environment and make a significant contribution to achieving sustainable building goals, such as those prescribed by the U.S. Green Building Council’s LEED building rating system. SCMs contribute to LEED credits in the following categories: Sustainable Sites, Energy and Atmosphere, Materials and Resources, Indoor Environmental Quality, and Innovation in Design.Cementitious blends have many properties that contribute to sustainable construction. Their use results in stronger, longer-lasting concrete and reduced emission of greenhouse gases. They also beneficially reuse by-products from other industries that might otherwise be disposed of in landfills. There are two main categories of blends: binary and ternary. Binary is a mixture of portland cement and one SCM. Ternary blends are a mixture of portland cement and two SCMs.
Performance benefits
SCMs impart a wide range of exceptional properties to concrete, which are particularly sought after by construction professionals. While the advantages to concrete in its plastic state are quite numerous (workability, finishability, etc.), perhaps the greatest benefits imparted by SCMs can be seen in the hardened properties.
Enhanced strength—SCMs contribute to the strength gain of concrete. Typically, slag cement and fly ash will lower early strengths (1 to 14 days) but significantly improve long-term strengths (28 day and beyond), depending upon the proportions and materials used. For example, Class F fly ashes tend to have a slow strength gain curve contributing mainly to the strength beyond 28 days, whereas silica fume contributes primarily to strengths at 3 to 28 days. Both compressive and flexural strengths can increase markedly at 28 days and beyond with the addition of SCMs.
Reduced permeability—SCMs significantly extends the life of concrete by reducing permeability to chlorides and other aggressive agents, especially at later ages. Silica fume has a very profound effect on permeability, exhibiting as much as a five-fold reduction in permeability. In concrete structures, permeability is generally the critical factor affecting durability.
Resistance to alkali-silica reaction (ASR)—SCMs can prevent excessive expansion and cracking of concrete due to ASR. The amount of slag cement required depends on the nature of the slag cement, the reactivity of the aggregate, and the alkali loading of the concrete. In most cases, 50% slag cement is sufficient with highly reactive aggregates. The amount of fly ash required typically is in the range of 15 to 55%, depending on the chemical composition of the ash, reactivity of the aggregate, and the alkali loading of the concrete. Generally, Class F ashes are much more effective in controlling expansion due to ASR than Class C ashes. Silica fume can control ASR; however, the amount required generally results in poor constructability. Blends of slag cement and silica fume, as well as blends of fly ash and silica fume, have a synergistic effect in mitigating expansion due to ASR, while producing a very workable concrete.
Resistance to sulfate attack—Sulfates, which are present in seawater, wastewater, and some soils, can react with the alumina in portland cement, causing expansion. SCMs offer superior resistance to these attacks because they contain fewer of the compounds that react with sulfates and because their low permeability keeps sulfate-bearing waters out. Typically, slag cement, silica fume, and Class F fly ashes are very effective in improving sulfate resistance. The effectiveness of Class C fly ashes is dependent on the ash chemistry and the replacement level.
Resistance to thermal stress—If the temperature differential between the concrete’s surface and interior is too high, cracking and loss of structural integrity can result. High replacement levels of slag cement and/or fly ash in properly proportioned mixes can reduce the peak temperatures as well as the rate of heat generation. Reducing the heat of hydration of the mix can moderate the development of thermal stresses within the concrete and prevent cracking.
Next-generation cements
The environmental movement in general—and strong interest with LEED certification in particular—will continue to drive the demand for sustainable construction materials that lower the carbon footprint of our built environment. One proven solution for reducing greenhouse gases per ton of cement—without sacrificing performance—is portland limestone cement (PLC).
One proven solution for reducing greenhouse gases per ton of cement—without sacrificing performance—is portland limestone cement (PLC).
Widely used around the world for decades with satisfactory performance, PLC contains between 6% and 15% interground limestone. In the U.S., ASTM permitted up to 5% limestone in portland cement in 2004 (ASTM C595), with AASHTO following suite in 2007 (AASHTO M240). At that time, it was estimated that these changes would reduce energy consumption by 11.8 trillion Btu’s and carbon dioxide emissions by more than 2.5 million tons per year.
In response to increasing calls to reduce the carbon footprint of the building sector even further, ASTM C595 and AASHTO M240 were revised in 2012 to allow up to 15% limestone in portland cement. These changes resulted in a new Type IL cement classification, which provides similar strength development, durability, workability, and other properties as Type I and II cements.
With Type IL cement, similar percentages of SCMs can be used in concrete mixes while also replacing up to 15% of the portland cement with limestone. This results in an additional 12 percent reduction in green gas emissions associated with the production of portland cement clinker. When combined with 40% to 50% SCMs, the effective reduction in the CO2 footprint of concrete is highly significant.
Materials do matter: Building a better world together
While the performance benefits of SCMs are quite numerous, their effect on the trend toward ever more green construction practices cannot be overstated. Specifiers, architects, and property owners are clamoring for buildings that are not only attractive, durable, and low maintenance, but also energy efficient and eco-friendly.
At Holcim US, our people across the country collaborate with customers to meet these stakeholder demands with a reliable supply of high-quality SCMs, blended cements, PLC and other innovative solutions. Contact your local Holcim sales representative to learn more about how our LEED-accredited professionals and technical teams can assist you with detailed recommendations on using these products to achieve high-performance sustainable construction goals.
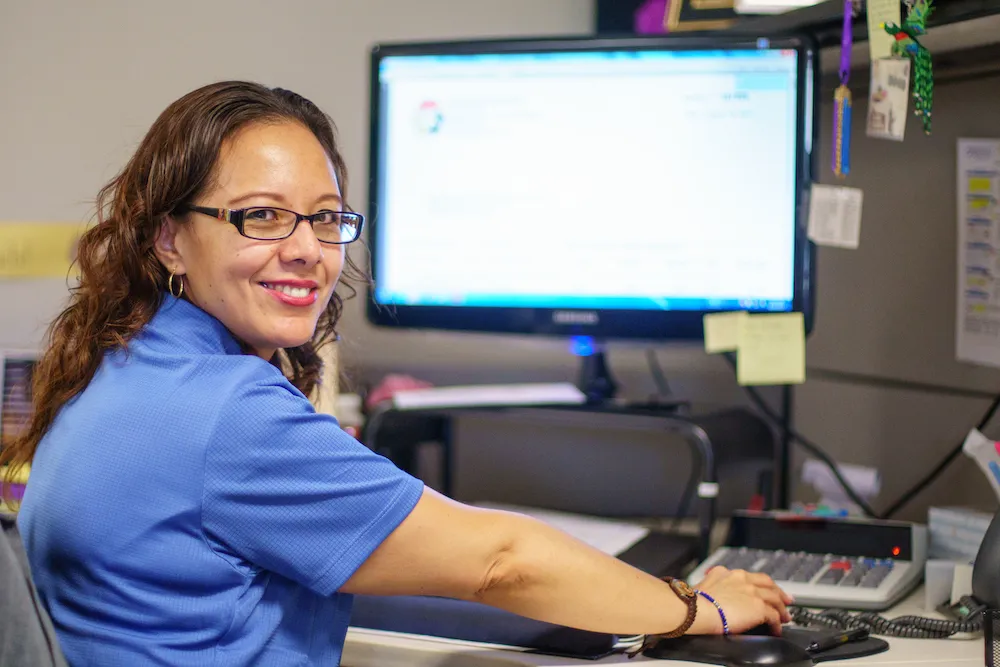
Have a question?
For more information on our technical services, or if you need guidance on your next project, please contact your local sales representative.